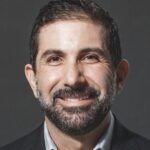
David Sciarrino
I was first introduced to the startup and commissioning process when I was working as a controls design engineer fresh out of college and I didn’t know $#!+.
We were commissioning fan-powered boxes, some of the simplest devices in an automation system. The boxes had power, but there was no air blowing from the air handler. I was there to learn from the two, yes two, control techs. One tech manned a laptop and the other climbed up and down the ladder to the box handing in the ceiling. Once plugged into the thermostat, each of the parameters for that box was manually entered using the laptop while the other waited. Things like: application, address, min/max flows, etc were entered. After that 10-minute startup process, the tech ran up the ladder and watched the damper move as the tech with the laptop commanded it. They did the same for the electric heat listening for the relay closing. They repeated that process 10 more times in the four hours I was there, noting the boxes that failed in some aspect to work as expected. That is less than 3 fan powered boxes per hour. That was my introduction to startup and commissioning, and I remember thinking to myself, “Wow, this is really slow and inefficient.”
The reality is, that process was extremely inefficient even to 20-year-old standards and incomplete considering air was never blowing.
If we fast-forward 20 years, a lot has changed. We can now take our design parameters and load them into all of the controllers in a project from one central location. That saves an enormous amount of time for startup, but much of the commissioning process hasn’t changed.
Someone at a factory had to install and wire the controller to the box correctly, install a damper actuator properly and torque it down so it doesn’t slip. After the boxes are hung in the ceiling, someone has to wire up the communications between the controllers correctly. If polarity was switched, or they skipped one, it won’t talk. Then an air balance contractor visits each box and controller to manually calibrate the airflow sensor. Although we can do things faster today, the human factor leaves a lot of room for error. Finally, after all the above is completed, the box and controller still need to be commissioned to verify that it works properly.
The reality is, many control contractors still commission systems in a similar manner to what I experienced 20 years ago. We still see technicians (typically one now) visiting these controllers, commanding dampers and valves, and looking at air flows and temperatures to ensure that everything is working as designed. That process can still take 10-15 minutes per box and is still subject to human error. Seeing that labor is the most expensive component in a controls project we need to find a way to make this process more accurate and less costly.
We are living in the world of analytics, AI, and machine learning and we are finally starting to see the commissioning process adopt those technologies. The key to making this work is designing the system in a virtual engineering environment that understands how the system should work in the real world. If you think this sounds like a form of digital twin, you’re right!
I’ve said before that a Digital Twin is more than just a virtual representation of data. It also needs analytics/AI and a common way to communicate between the virtual and physical worlds.
I have recently worked with CUBE Box, a software platform by CUBE USA that does exactly that. This technology compares the engineered system in its virtual environment to what it sees in the physical space during and after installation.
Immediately, there are multiple cost savings advantages using this software:
- Identify omitted or superfluous Devices: Every controls job I’ve project managed had devices that were in the design that never got installed or additional devices that were installed that weren’t in the design. Eventually, these get found after the building is occupied and there’s a hot/cold call. Rather than an expensive warranty call, flagging these anomalies automatically lets someone address it early.
- Communication issues: Using this technology for commissioning will tell you right away which devices are not communicating. It’s easy to ignore something that doesn’t show up at all.
- Field changes: Although device and point names should be followed based on the design documents, things change in the field. Technology that can identify when a device is missing and pair it up with the same device with a new name makes resolving anomalies painless.
- Automated commissioning: Finally, using fault detection and analytics, this technology will determine what specific devices on certain boxes or systems need to visited by a person to resolve issues. No need to manually check every device because it has been interrogated and tested by the software to work as designed. A punch list is managed in real-time and can be viewed by anyone involved in the project.
Once the project is completed, CUBEBox doesn’t take a back seat. Days after a building is turned over to new owners, changes can be erroneously made in the automation system taking devices or systems out of their design parameters. But, if you continuously commission, those problems will be identified immediately and can be corrected to bring the building and its systems back into design and keep them there. Visit the cube-usa.com to learn more about this platform.
CUBE-USA creates software for controls contractors that supports their teams with estimating, labor forecasting, schedule management, CRM, and now automated building commissioning.
What are you commissioning stories and how do you see things like Digital Twin changing the way we design and interact with the built space?