An interview with Roberta Tincher, Utilities Systems Manager, University of Kentucky. As one of Tridium’s first big education campus customers and a speaker at one of its first Niagara Summits in 2004, Bobbie will be a special guest presenter at Niagara Summit 2024 next month. Come to Anaheim to meet Bobbie and hear more about her journey in building automation and controls.
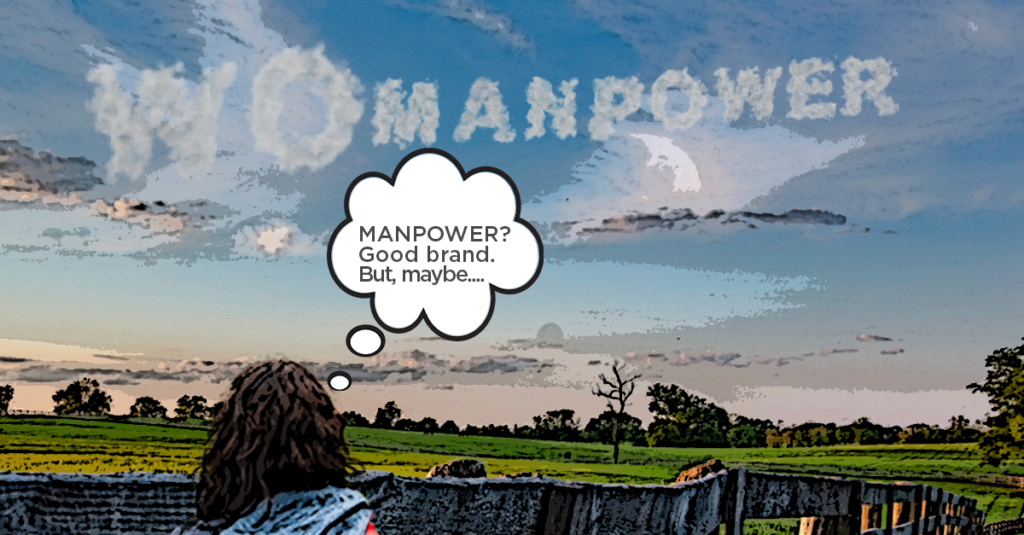
Therese: Tell me everything. Start from the beginning.
Bobbie: I grew up in a little small town in Kentucky. Bluegrass region. Gateway to the mountains. After graduating from high school, I opted to study Computer Science and programming at the University of Kentucky. I earned my bachelor’s degree from the UK’s School of Engineering, and then went to work for a company called Manpower of Central Kentucky. To keep communications and data flowing among all the offices of that regional entity of the global staffing firm, lots of IT networking was needed, which I knew nothing about. But I learned quickly, and I stayed there for three years. I networked all the Ohio and Kentucky offices. I also gained experience as a trainer, leading forums about how to do networking work and even some sales training.
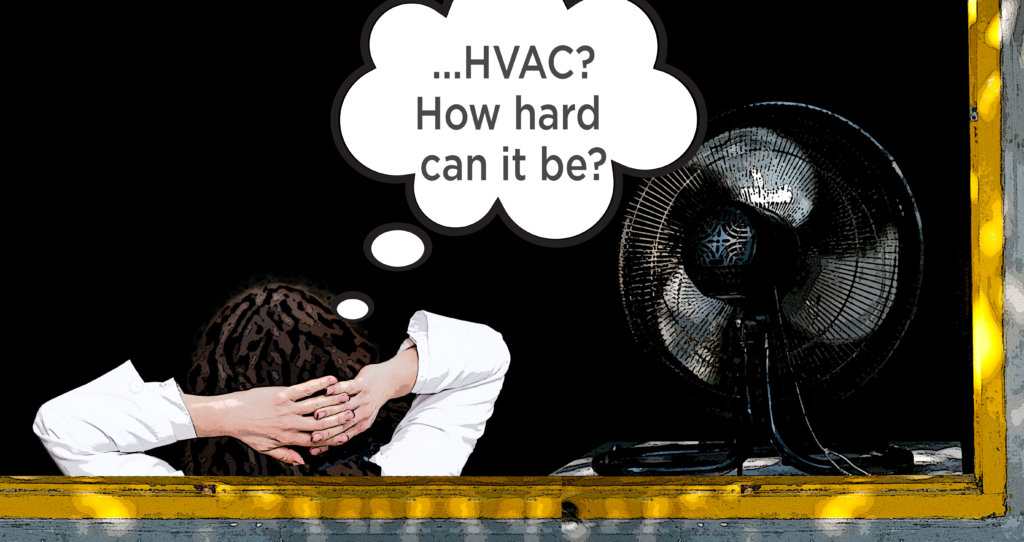
Therese: But, then your alma mater called you back home?
Bobbie: More or less. While at Manpower, I saw an information systems job posted by the University of Kentucky, and I applied. The interviewer asked whether I knew anything about HVAC, and I said, “Well, we sat a box fan in the window when I was a kid. If it was hot outside, it circulated hot air; and if it was cold, it pulled in the cold air.” Maybe he thought that was funny, but that interviewer – he was the then Director of Physical Plant Division, Ed McClure – hired me right away. That was 2002 and the start of my first job in building automation.
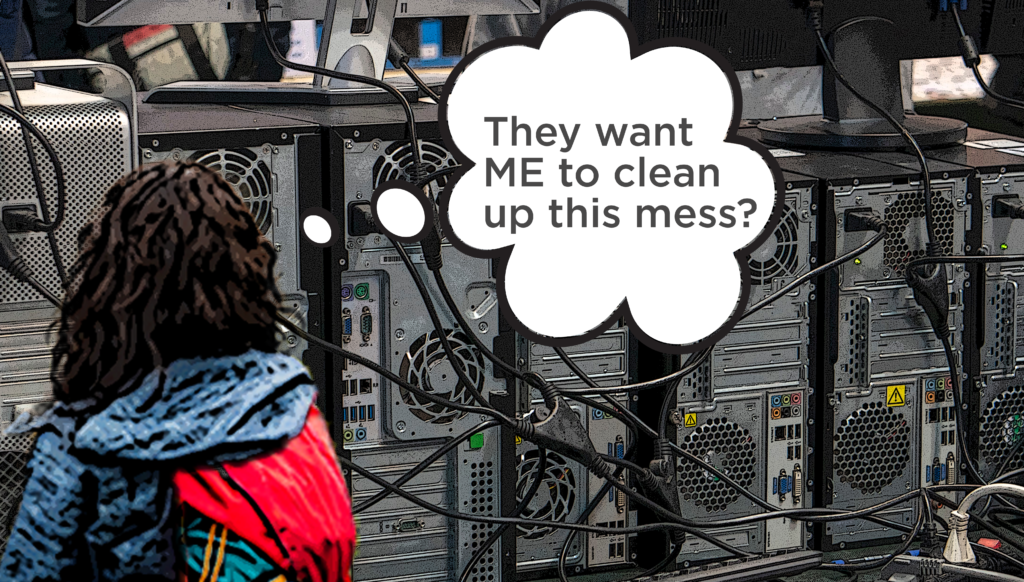
Therese: Was it a big leap to transition from the IT networking world of Manpower to the Operations Technology at University of Kentucky?
Bobbie: UK Facilities was and remains a fast-paced, complex operation. Ed McClure was a forward thinker. I started at the UK Medical Center physical plant. When I arrived, there were numerous building management systems, from the big brands of the day. The hospital had an old DDC system comprised of hundreds of network control modules. Dispatchers were looking at different screens. Nothing was online. Ed had already purchased Tridium’s early R2 version of Niagara Framework. So, he handed me the CD that held the software and said, “Your job is to bring everything together and online. You know what to do. Just go make this work.”
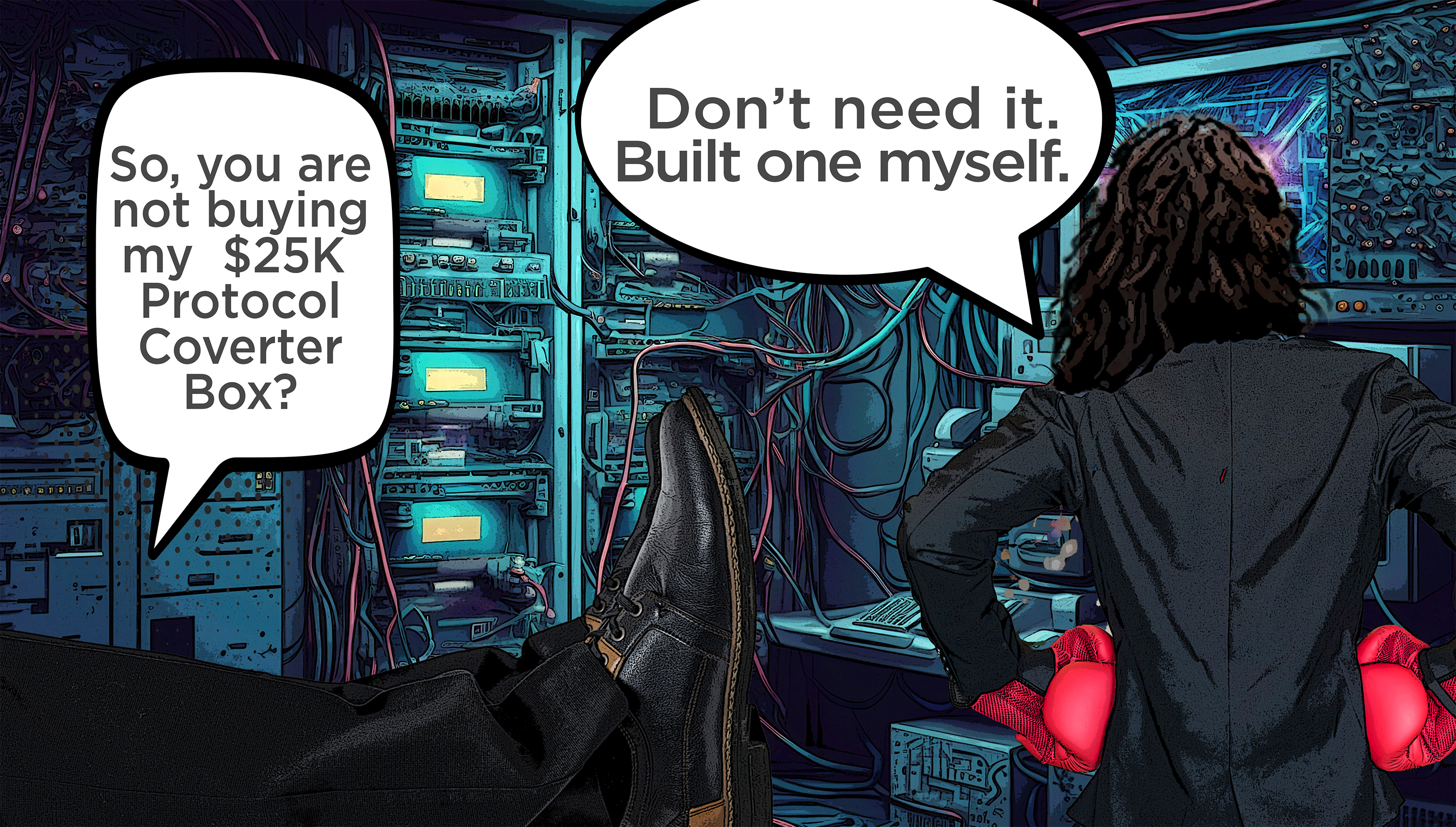
Therese: So. it was that simple. You did it. Story ended. Happy ever after.
Bobbie: Not simple. No. Not over either. But I did just dive in. I had to get a universal network controller which was, at the time, like a big JACE. One of those big old, blue panels. I put that on the network. Then I had to bring all the control modules from the old DDC system over, pulling and naming each point manually. Ultimately, I could export these points to my R2 server. Bringing the power stuff online was one of the easier integrations. There I could use a BACnet gateway to an APOGEE server. However, I also needed to migrate from our big-brand BMS systems to R2. Here the obstacles were less technical and more economic. I did not have the budget for what that vendor wanted for its protocol conversion equipment. I called around and found out that Contemporary Controls could supply all the necessary parts to make our own converter box. All I needed from the big brand was a card – available for about one-fifth the cost? How about that?
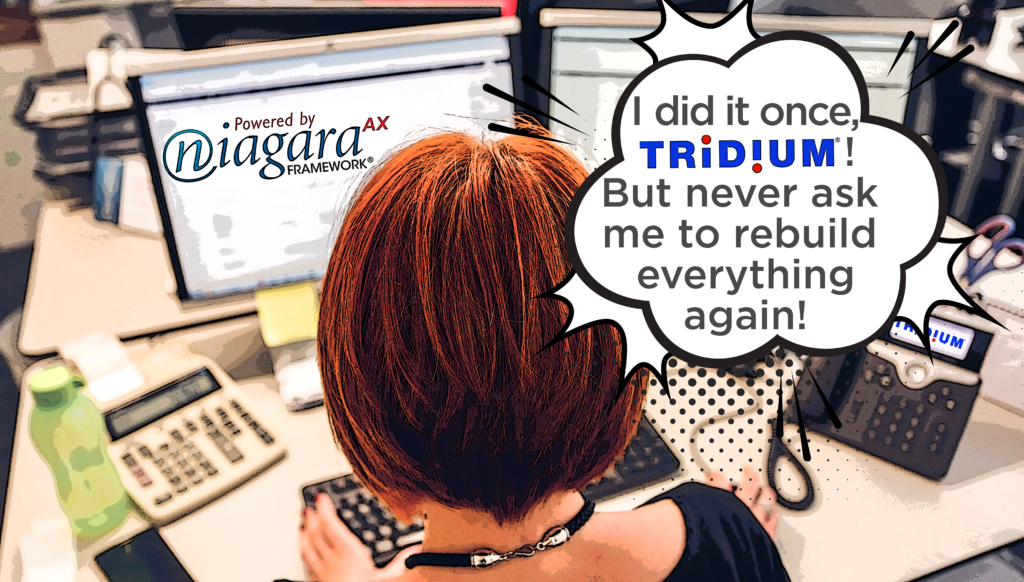
Therese: So now, you’ve reached the point of ‘building automation conquered.’ Happy ever…
Bobbie: Hmmmfff. I put many buildings onto the R2 network, and I built out a UI that I was happy with, yes. However, fast forward a few years, and Tridium introduces Niagara AX. I was hesitant to move past that R2 version of Niagara. It took some convincing – mostly from Tridium’s lead engineer/architect Kevin Williamson. Eventually, I did move the Med Center onto Niagara AX. For that R2-to-AX migration, I needed to rebuild all the graphics. It was a lot of work. I told Kevin at that point, “If we have to do this again, you better make it so that I don’t have to rebuild everything!” When it was time to migrate off AX to Niagara 4, we didn’t have to rebuild the graphics. I guess Tridium Engineering heard my message. Kevin has been one of my biggest supporters inside Tridium over the years. Everything I’ve called about and identified as problems, and everything I’ve wanted to try, he has supported from the inside.
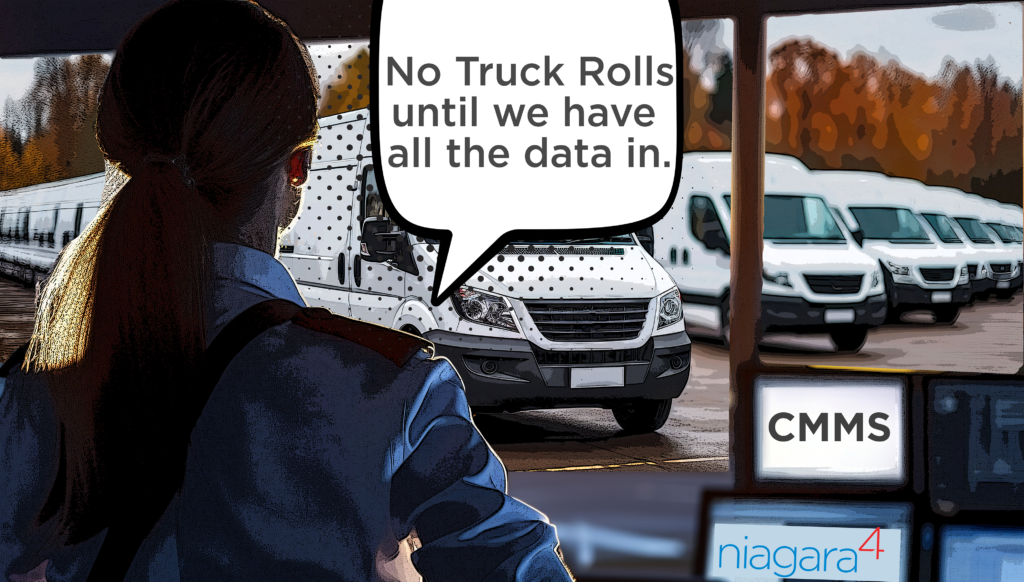
Therese: University of Kentucky has helped Tridium evolve Niagara in the right directions.
Bobbie: An area where I have been pushing from the start is around graphics and reports. For example, when our customers were starting to forget about their pagers and rely upon their personal mobile devices, we wanted alarm info sent via texting and emailing. We can do this from Niagara now. Integrations are another important area. We wanted Niagara to integrate with our work management system, and today it does. Every time Niagara detects an alarm situation that requires staff attention, it generates a notification in our work management system. Our dispatchers do not have to type in the information. We get to action and resolution much faster and we can better prioritize the work. In fact, we can program Niagara to classify alarm scenarios and assign priorities before the work order is generated and sent. That’s a huge time-saver.
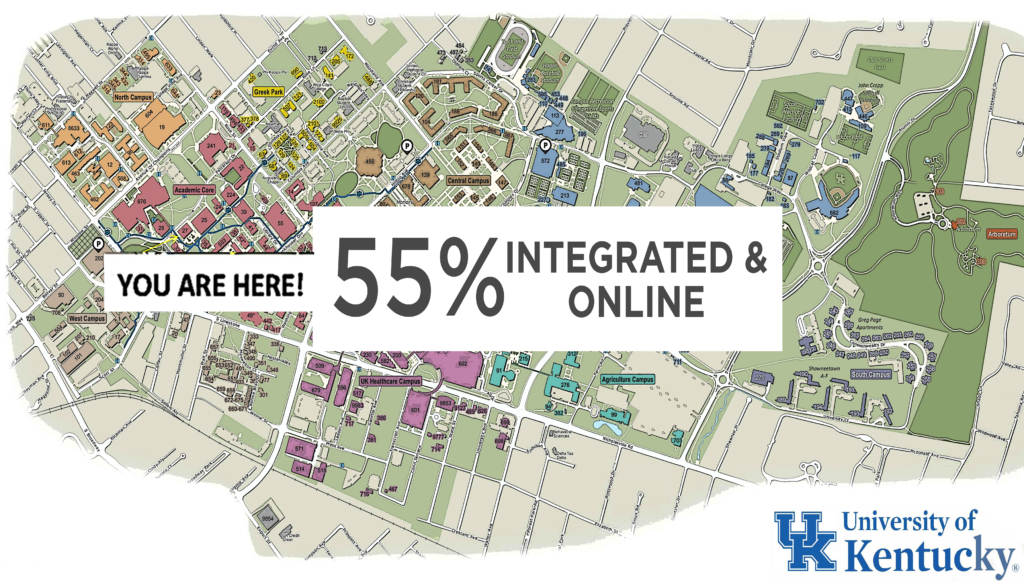
Therese: In 2002, when Ed McClure asked you to “Bring everything together and online,” that was a big charter! How’s that going?
Bobbie: We had a unified system online within my first year at UK. That was 15 big devices on 3 different systems. That took lots of interaction with IT. No leaning on default settings. Setting and following our own guideline spec. Today UK has over 5000 devices on the Niagara network campuswide. Our Medical Center — three hospitals and our research facility, plus classrooms – are all online and under Niagara supervision. We are still integrating every day. We are about 55% done with bringing in campus devices into Niagara 4. Ed McClure retired about three years ago. At that time, I got the call to come over onto the main campus and do what I had done at Med Center; that is, lead automation and controls for the whole UK campus. The university regents could see the results of the integration work in the buildings we had completed in terms of fewer hot/cold calls, more energy savings, etc.
We still have three networks on our system: our Niagara network, a BACnet network to legacy equipment like the big-brand BMS system that was in place when I arrived, and an OBIX network. I think many folks in the industry don’t really understand all the IT background stuff that has to happen when you have a system that operates according to different methods and supports multiple DBMS. We have branded controllers that are BACnet-over-IP devices that can be integrated to send data straight to Niagara. We also have added BACnet controllers from various manufacturers. We are tracking our instance numbers and our IP addresses – we track all that information. We work with our IT network folks to try to get this stuff on our own VPN, so that we’re not on the data LAN and there’s less traffic overall.
Now that we are about 70% done with the campus buildings, we are starting to integrate the utility plants. Getting these online is a big challenge because a lot of the operations in the utility plants have been done manually for years. For example, staging chillers has been manual. An operator monitors the situation, and occasionally he will call in with the report and request, “My air handlers are hot. Please turn on another chiller.”
Well, that’s not completely efficient because, while the air handlers might be hot, more chilled water might not be the solution. We’ve had calls for more chilled water when it was 34F degrees outside. We need to know the answers to questions like “Is the chilled water valve the first valve into the building? Is that working? Are the fan coils clean? Are the dampers working? Why aren’t you using free cooling?” These questions were never really asked before. Our building engineers and BMS programmers who are working out the automated approach, they think through these questions and potential answers. A good Sequence of Operations program – fed the right data- can pull all the answers in. Then we need to train our maintenance teams to understand what the programs are meant to do and how the whole automated system is supposed to work.
You need to build a lot of trust across the whole team. You also have to prove yourself constantly. Anyone trying this should expect a struggle.
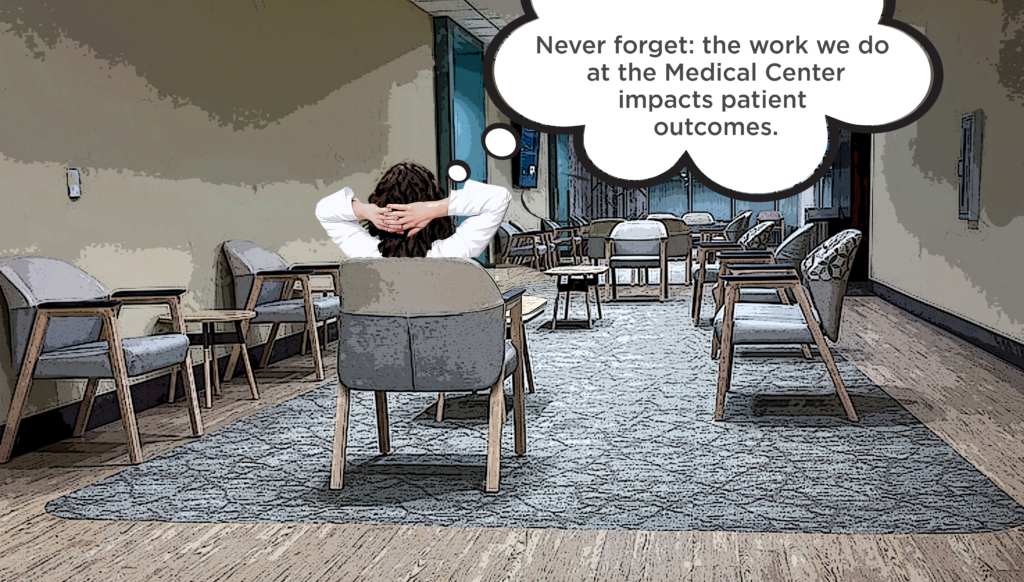
Therese: What motivates you to keep out ahead when it comes to using data to run facilities operations across the campus?
Bobbie: Resiliency is huge. Building services in a Medical Center cannot go down. My mother was a patient here when I was young. Sadly, she died from breast cancer when she was only 51. When I first started working here, I didn’t want to go to the Market Cancer Center. I didn’t want to go in that building. I didn’t want to have anything to do with that building. But, once I was bringing that building online, I learned more and more about the cancer research they do there. I began to connect personally with my job, recognizing that I had a part to play in supporting the success of that research.
On the Medical Center side, the sequences that control air handling operations become even more precise and complicated because now, they are not just about energy saving, they are about life saving. We need to maintain outside airflow volume to the degree required not just by building code but by what the medical books say. By ‘Doctor’s Order,’ places like Burn Units and Surgery Rooms need negative air. Return humidity needs to be in a certain zone. In one place, we will hear ‘We cannot have CO2 here. Then in other places, especially with Covid 19 concerns, we are asked to supply 100% outside air. It is a struggle to get the fans right to deliver the right mix.
The pandemic was another experience that tested us all to the extreme. When the Covid vaccine came out, we were the first ones to get the call from the UK Medical Facilities team: “We need our refrigerators monitored.” We caught a lot of the hospital folks calling our Tridium system “central monitoring.” They would say, “These code vaccine refrigerators and freezers must be on central monitoring. Call Bobbie!” With Niagara, we were ready for that. We made sure that they were monitored and that they were alarmed.
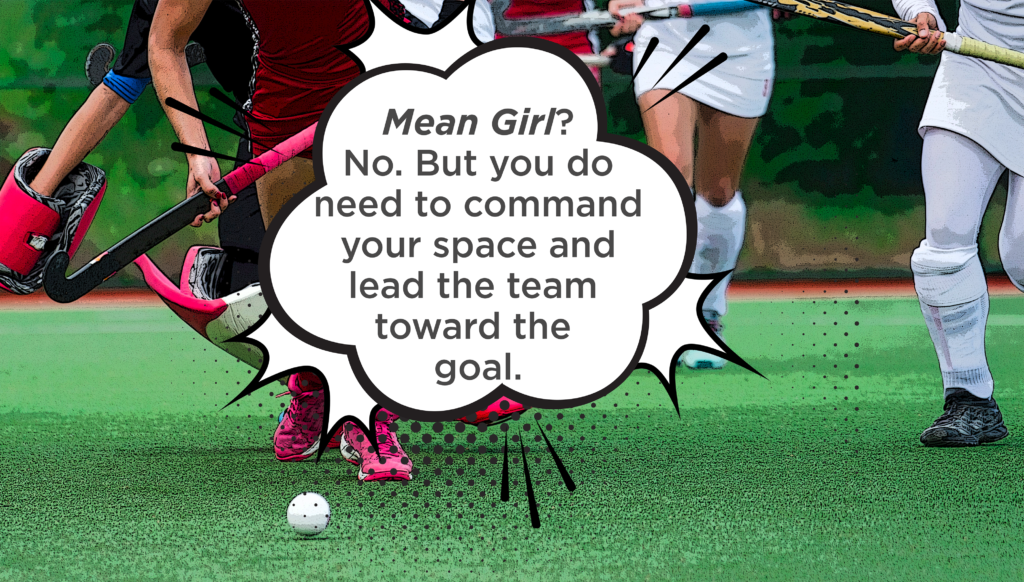
Therese: What a journey! You started as a Level 4 Tech and now you’re managing an entire campus. Do you have any advice for other young people starting out in this industry.
Bobbie: When you are young, there is a tendency to try to prove that you can do things, make things happen. You question or just don’t see the barriers your predecessors considered insurmountable. For a young woman, maybe more so. At least that was the way I was. Vendors and contractors back then may have told you that I was just mean. So maybe I was?
I have faced constant and tremendous pushback at every turn. As we moved forward with Tridium’s Niagara system, a lot of our other vendors pushed back because they were just not as advanced on open-protocol technology, and they were not as concerned about keeping up with the ASHRAE guidelines on openness as we were. You know they had their proprietary systems, which worked well. And, they had plenty of other customers that weren’t as ‘mean’ as I was. They were doing their own thing, and they were making a lot of money at it. I was often up against the attitude of ‘Why do I need to change it for you?’ Their dismissal of me just made me even more determined to prove myself.
My advice is to be tenacious, but also to listen to your mentors and to keep asking questions of any of your peers that might be in your same shoes.
Today, I’m not motivated to prove anything to anyone else. At the University of Kentucky generally, we strive to graduate students and heal patients. Even if you are Facilities. Our job is to make sure that patients and students are comfortable and that their rooms are quiet for healing or for testing, or whatever else is right in terms of outcomes. And yeah, we have this Tridium system, and I do the building automation. I may turn things off at night when the building isn’t in use or otherwise do things to save costs. But, even that, all of it is in service to the UK Community. Our success is measured in terms of this student being able to concentrate and pass that test, or this patient feeling better, or this researcher finding a cure. We recognize that our role is key to those successes.