Introduction
In the dynamic field of facility maintenance, especially in areas like HVAC and BAS (building automation systems), decisions to embrace change are driven by technological advancements and the need to optimize operations, enhance efficiency, and improve occupant comfort. One such pivotal decision is the implementation of a new BAS. This article delves into how the benefits of such a change when carefully weighed against the costs, can lead to a substantial long-term value addition to facility operations.
Understanding Costs and Benefits
The initial cost of a new BAS often includes the purchase price, installation expenses, and training for technicians. However, realizing that the benefits can significantly offset these initial costs over time is crucial. Key benefits include:
1. Energy Savings: Advanced BAS can lead to more efficient HVAC operation, reducing energy consumption and lowering utility bills.
2. Improved Occupant Comfort: A well-integrated BAS ensures optimal indoor climate control, enhancing comfort and potentially increasing workplace productivity.
3. Remote Monitoring and Control: This allows for real-time adjustments and monitoring, leading to proactive maintenance and reduced downtime.
Calculating Long-Term Value
To determine the value of a new BAS, subtract the total initial costs from the long-term benefits. These benefits also include:
• Extended Equipment Lifespan: Optimized operations mean less wear and tear on equipment, extending its useful life.
• Reduced Downtime: With predictive maintenance capabilities, a BAS can foresee potential issues, reducing downtime and repair costs.
• Increased Occupant Satisfaction: Comfortable environments can lead to higher satisfaction among building occupants, which can be pivotal for commercial spaces.
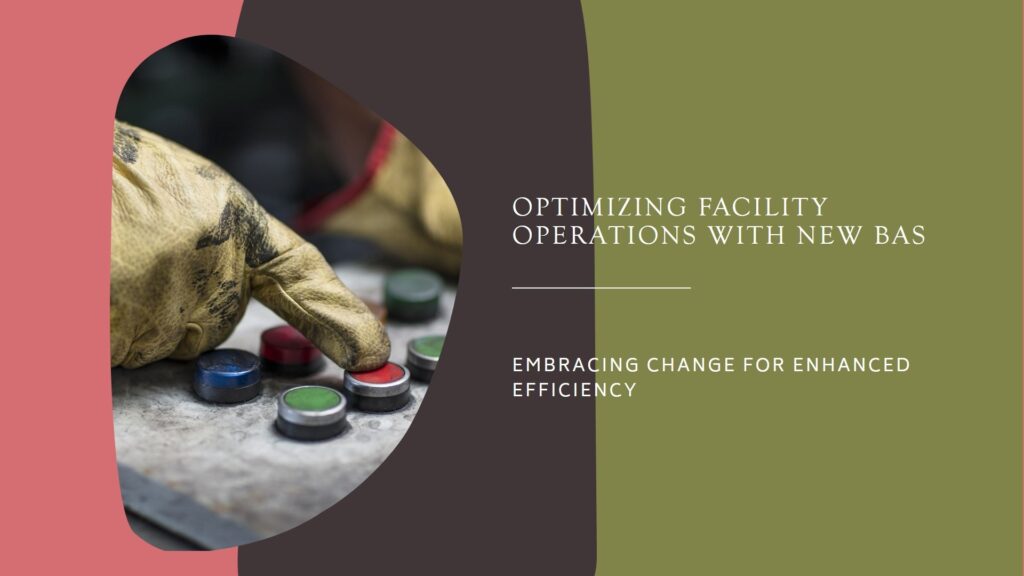
Case Study: XYZ Corporation
Consider the example of XYZ Corporation, which implemented a new BAS in its headquarters. The initial investment was substantial, but within a year, they reported a 15% reduction in energy costs. Additionally, the system’s predictive maintenance feature reduced equipment failures by 20%, significantly decreasing downtime and repair costs. Occupant feedback was overwhelmingly positive, noting improved comfort and air quality.
Conclusion
A detailed cost-benefit analysis should underpin the decision to implement a new BAS in facility maintenance. While the upfront costs might seem daunting, the long-term benefits—from energy savings to improved occupant satisfaction—can add significant value. This strategic approach ensures that facility maintenance technicians are not just reacting to technological changes but are actively leveraging them to enhance their operations, aligning with the overarching goal of continuous learning and improvement in the field.