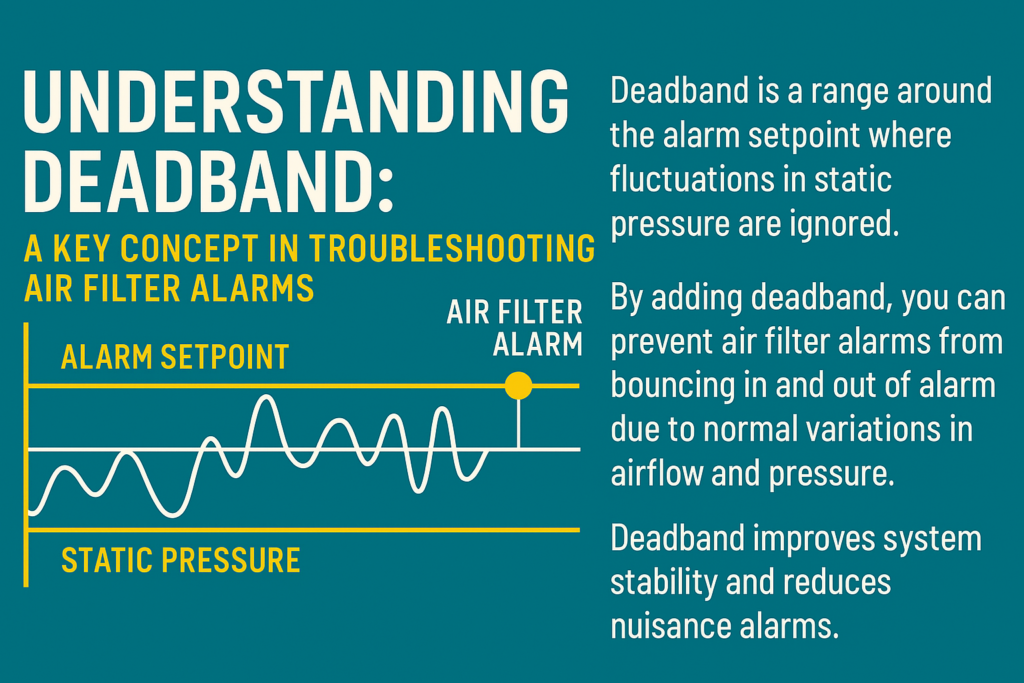
Precision in Alarm Logic: A Deeper Look at Deadband and Time Delay
In facility management, especially within HVAC and Building Automation Systems (BAS), the difference between a well-functioning system and one plagued by false alarms often comes down to how well we understand and configure two core parameters: Deadband and Time Delay.
These features are not just settings buried in software — they are decision-making rules. They tell the system when to speak up and when to stay quiet. As we’ve recently encountered during troubleshooting of a lingering air filter alarm, failing to align these two settings with actual system behavior can lead to confusion, wasted labor, and system inefficiencies.
This article aims to clarify what deadband and time delay really are, how they work together, and how to fine-tune them to support reliable and meaningful alarms.
Deadband: The Quiet Zone Between Fault and Normal
Definition
In BAS terms, deadband refers to a defined buffer zone between a fault threshold and the normal operating range. It tells the system: “Don’t reset the alarm yet — let the condition stay clearly normal for a while.”
It prevents rapid toggling of alarm states due to natural, harmless fluctuations. This is especially important for analog values like temperature, pressure, or humidity, which often hover near thresholds.
How Deadband Works
Take the case of an air filter differential pressure (DP) sensor:
- High Limit (Alarm Trigger): 1.00 in H₂O
- Deadband: 0.10 in H₂O
- Reset Threshold: 1.00 – 0.10 = 0.90 in H₂O
If the filter’s pressure rises above 1.00″, the system triggers an alarm. But that alarm won’t reset unless the pressure drops below 0.90″, ensuring the system has truly returned to a healthy state.
Without deadband, the alarm might flicker on and off when the reading floats around 0.99–1.01″ — causing confusion and possible alarm fatigue.
Troubleshooting Tip
If you’ve replaced the filters but the alarm still won’t clear, check the deadband. If the DP drops just under the high limit but not enough to satisfy the reset condition, you might need to reduce it.
Time Delay: The System’s Patience Meter
Definition
Time delay defines how long a fault condition must persist before the system reacts. It can apply both to activating and clearing an alarm.
Rather than reacting instantly to a spike in DP, time delay says: “Let’s make sure this isn’t just a short-term fluctuation before we trigger an alarm.”
How Time Delay Works
Let’s revisit our air filter DP sensor:
- Current DP: 1.02 in H₂O
- High Limit: 1.00 in H₂O
- Time Delay: 300 seconds (5 minutes)
Even though the pressure exceeds the limit, the alarm won’t trigger unless it stays high for 5 continuous minutes. If it returns to normal before then, the system discards the event.
Likewise, a time delay can apply to the alarm reset: even after the pressure falls below the reset threshold, the system waits to see if it stays there for the full delay period.
This is especially useful for fan startups, VFD ramp-ups, or dirty airflow transitions where pressure values momentarily spike.
Working Together: Deadband + Time Delay
When used correctly, deadband and time delay complement each other beautifully:
Function | Deadband | Time Delay |
Filters value-based noise | Yes | No |
Filters time-based noise | No | Yes |
Prevents quick flickers | Yes | Yes |
Applies to analog signals | Yes | Yes |
Applies to digital inputs | No | Yes |
For air filter alarms, here’s how they cooperate:
- Deadband ensures the pressure has truly dropped below the fault range.
- Time delay ensures the pressure has stayed there long enough to be trusted.
Real-Life Example from the Field
Scenario: After replacing filters, the DP reading dropped to 0.73 in H₂O. However, the alarm did not reset.
Initial Settings:
- High Limit: 1.00 in H₂O
- Deadband: 0.23 in H₂O
- Reset Threshold: 1.00 – 0.23 = 0.77 in H₂O
- Time Delay: 600s (10 minutes)
Issue: Even though the value was under 1.00″, it wasn’t below 0.77″. Also, the 10-minute delay meant we had to wait a long time before seeing any changes on the graphic.
Resolution:
- Adjusted Deadband to 0.10 in H₂O
- Adjusted Time Delay to 300s
Outcome: The alarm cleared within 5 minutes once the pressure stabilized below 0.90″. Problem solved.
Best Practices for Tuning Deadband and Time Delay
- Understand the system behavior
- Review how your equipment naturally behaves during normal and abnormal conditions.
- Review sensor data trends
- Use your BAS trend logs to analyze how quickly conditions change.
- Start conservative, then tune
- Begin with wider deadband and longer delays during commissioning. Tighten as your confidence grows.
- Document every change
- Log adjustments in your Knowledge Hub or CMMS. Include the reason and result.
- Collaborate with EMS/BAS team
- Alarm logic is typically software-based and must be updated in the controller logic, not the sensor.
Final Thoughts
Deadband and time delay are often overlooked, yet they are central to accurate alarming, trouble-free maintenance, and system trustworthiness. By mastering these parameters, we shift from reacting to alarms to designing smarter responses.
In facilities where uptime and reliability matter, learning to fine-tune these tools gives us the edge—not just in preventing alarm noise, but in ensuring the system is truly speaking when it matters most.